From Wind to Hydrogen: What an Operating Green Hydrogen Plant Really Looks Like.
Published August 27, 2024 by Clayton Mathias on LinkedIn.
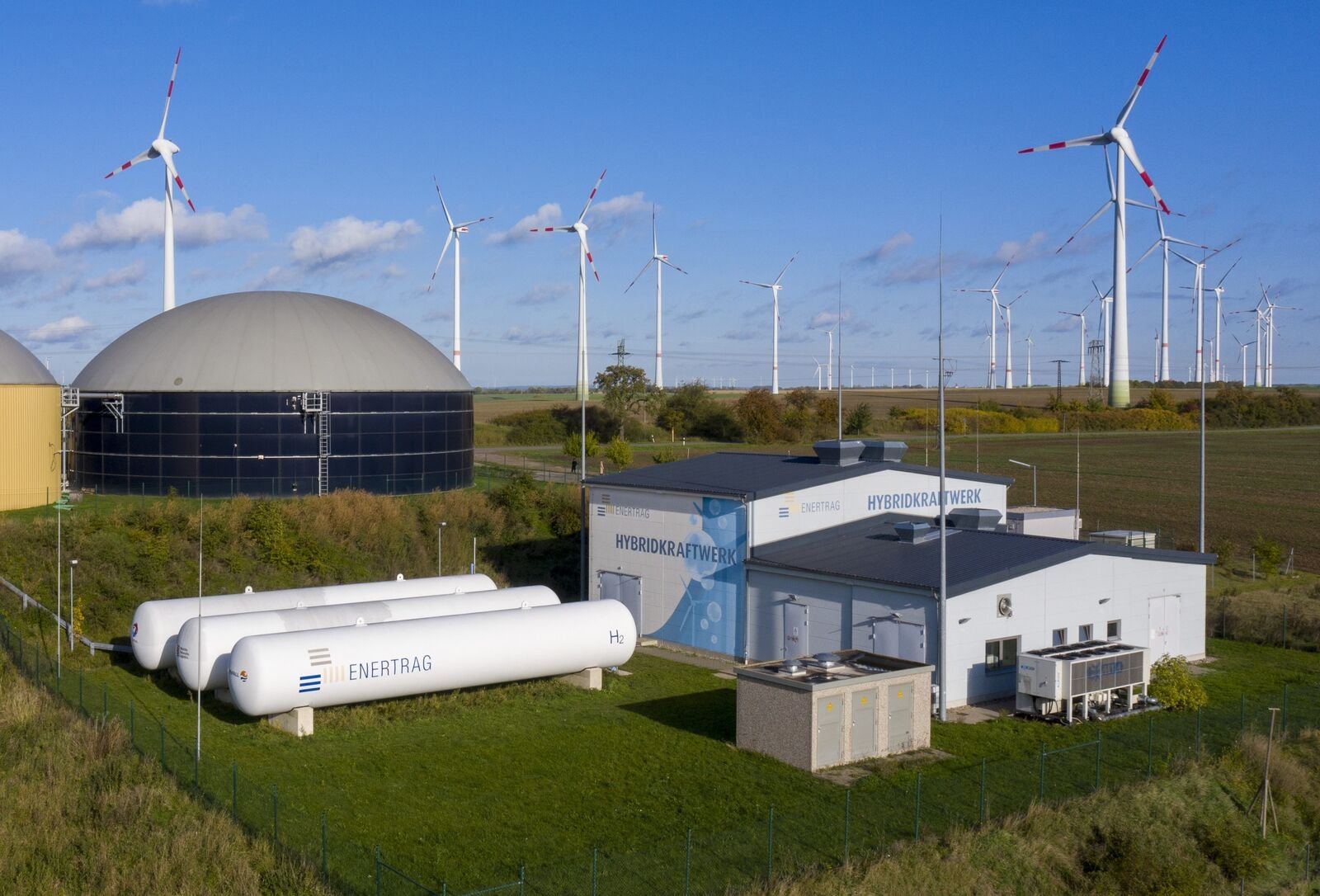
Image Credit: Enertrag/Silke Reents
If you're actively following the green hydrogen sector, it's likely you've seen the digitally created futuristic renderings of green hydrogen plants, overlayed at ports and industrial centers, with photoshopped solar fields and wind turbines in the background. But, what does an operational green hydrogen facility actually look like?
I'm extremely fortunate to have onsite working experience at an operating green hydrogen plant, powered by wind energy. It's at the Enertrag Prenzlau facility located north of Berlin, Germany. Having worked with Enertrag developing large scale green hydrogen projects internationally, I eagerly visited the Prenzlau facility on many occasions to satisfy my own curiosity, reviewing equipment and sketching up rough piping and process flow diagrams in my notebook. Whilst digging into technical specs with the plant operator or leading international representatives and delegates through tours of the facility, I'd admire the simplicity of the site, elegantly situated amongst canola fields, quietly producing its emission free gas; it's only neighbor, a renewable bio-gas plant also owned and operated by Enertrag.
0.56 MW Alkaline Electrolyzer, Image Credit: Enertrag/Silke Reents
Commissioned in 2011 the facility was one of the first commercial 100% renewable green hydrogen facilities of its kind. Powered by three 2.3 MW Enercon E-82 wind turbines as observed in the background of the cover image, it has the capability of producing 94,000 kg of annual hydrogen, via the 0.56 MW alkaline membrane electrolyzer. The electrolysis capacity is certainly in the smaller range by today's standards for large developments, but highly effective as an early proof of concept for a variety of commercial hydrogen use cases.
Reflecting on my background in Oil & Gas operations, what stands out to me is the simplicity of green hydrogen production. You take water and split it into its hydrogen and oxygen molecules, via an electrochemical process (electrolysis) powered by renewable electricity. It's the renewable electricity and water feedstock that yield an emission free hydrogen gas. Hydrogen is the energy carrier in fossil fuels, albeit they are attached to carbon molecules, which are harmful to the environment when released into the atmosphere.
In comparison to many legacy oil and gas processing facilities I've worked at, which require energy inputs like natural gas for heat, process chemicals, careful monitoring of upstream production volumes and retention time for processing, sour gas handling in some cases, disruptions and personnel call-outs due to ambient weather impacts and equipment failures, plus emissions from venting and flaring and the occasional onsite or upstream release or leak - comparing a green hydrogen plant to an oil and gas facility, would be like comparing a Tesla EV to a 1983 Ford Bronco. I owned a Bronco, so I'm a bit of a subject matter expert on its operational quirks, like the 4x4 hubs that were difficult to engage at sub-zero conditions, and whopping 26 l/100 km fuel economy.
My intention isn't to throw the Oil & Gas sector under the hydrogen fuel cell bus. I truthfully enjoyed working in that sector for almost two decades, and do believe has a place in our energy mix, albeit with further integrated energy efficiency and emission mitigation measures. But having developed an open minded interest towards energy transition, the analogy does seem kind of appropriate.
Annotated Facility Overview, Image Credit: Enertrag/Silke Reents
But back to the Prenzlau facility - in addition to it's normal operating load for base demand, when there is excess wind electricity that can be generated, rather than curtailing it, the electrolyzer can be switched on to produce additional gas. The electrolyzer discharges hydrogen at a pressure of 40 bar, where it's then fed through a purification & drier system, before being stored in above ground high pressure bullet style tanks. The hydrogen is commercialized through a variety of offtakes including injection into the regional natural gas grid, via an underground pipeline running adjacent to the facility. The natural gas system in Germany is already regulated to allow for pure hydrogen injection and blending.
An electric compressor with 400 bar max. discharge pressure, provides the necessary compression for cylinder and tube trailer filling, including distribution to hydrogen fueling stations, heat plants, and generators for grid stability reasons.
Enertrag Prenzlau Green Hydrogen Plant Specifications:
Commissioned and operating since 2011
0.56 MW Alkaline Membrane Electrolyzer
1,200 kg gaseous hydrogen storage at 40 bar (3 above ground gas storage bullets)
Low pressure compression for pipeline injection in the natural gas grid (<30 bar)
High pressure compression for bottle/trailer filling (40 bar suction, 400 bar max discharge)
Balance of plant: rectifier, MCC, reverse osmosis water treatment unit, buffer tank, hydrogen drier/purification unit
Hydrogen use cases: gas grid injection, reconversion to electricity and heat, hydrogen fuel cell vehicle fueling, cylinder and tube trailer distribution
Hopefully this article has provided you a glimpse of what an operational green hydrogen plant looks like and how it operates. There are few operational sites out there, but they do exist, and there are many currently under development. Certainly since its commissioning in 2011, advances in technology have seen similar capacity systems become quite compact, even being packaged into prefabricated standard size shipping container units. The Enertrag Prenzlau facility boasts all the same components as modern day systems, in a site layout that is easy to appreciate and understand. If you ever get the chance I'd recommend taking a tour, which is on occasion offered to the public through conference side events.
Enertrag is only one of a long list of players developing and positioning hydrogen projects internationally. Their proof of concept at Prenzlau adds tremendous credibility to the operational reliability, technological and commercial readiness of green hydrogen systems.
I am grateful to Enertrag for being part of my personal energy transition, and for the opportunity to have further developed my understanding of green hydrogen production operations with them.
This article is intended as an education thought piece. Images were observed to be utilized in the public domain in online media and articles by third parties, and were obtained from these sources with all references to Enertrag and the photographer expressed.
Read the next insight.